From Production to Construction - Steel
- AYBERK YAVUZ
- Sep 13, 2023
- 7 min read
Updated: Apr 13, 2024
Steel fabrication is an process that involves working with steel to construct various structures and components. It is of importance for structural engineers to have an understanding of the complexities associated with steel fabrication. This knowledge is vital as it not affects design considerations but also plays a role, in ensuring the overall durability, longevity and safety of any structure. Here are several essential factors to take into account;

Picture 1: Steel Frame
Raw Materials
Carbon Steel: Most commonly used; classified by carbon content and additional alloying elements.
Stainless Steel: Corrosion-resistant, used in environments where resistance to the elements is crucial.
High-Strength, Low-Alloy Steel: Provides better mechanical properties or greater resistance to corrosion.
Pre-Fabrication Processes
Melting and Casting: Steel production starts by melting iron ore, coal, and limestone in a blast furnace. Subsequently, steel is cast into shapes.
Rolling: Steel is passed through a series of rollers to achieve desired thickness and shape.
Coating: Protective coatings may be applied to enhance corrosion resistance or weldability.
Fabrication Techniques
Cutting: Methods include laser cutting, plasma cutting, shearing, and sawing.
Forming: Techniques like bending and rolling are employed.
Welding: MIG, TIG, and arc welding are common techniques. Consideration for heat-affected zones and residual stresses are crucial.
Machining: Drilling, milling, and turning operations might be required depending on design specifications.
Joining: Bolting and riveting are common non-welding methods for joining steel members.
Surface Treatment: Processes like sandblasting, painting, or galvanizing can be applied to improve appearance, adherence, or corrosion resistance.
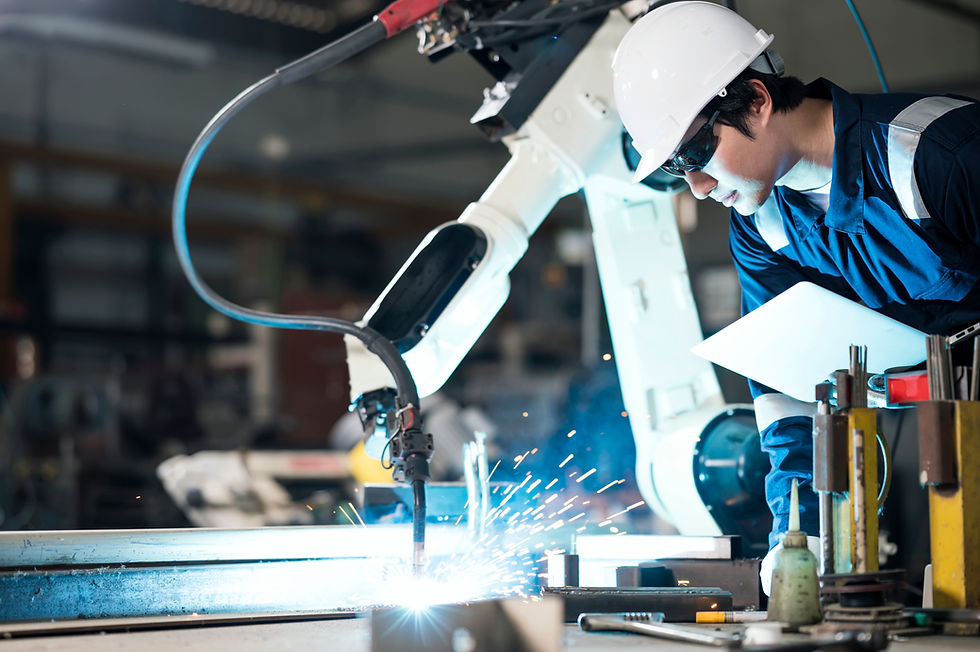
Picture 2: Fabrication process of Steel
Quality Control
Material Inspection: Ensure that the received material meets the specified ASTM or other international standards.
Dimensional Checks: Verification of dimensions before and after fabrication steps.
Weld Quality: Inspection techniques include ultrasonic testing, magnetic particle inspection, and dye penetrant inspection.
Documentation: Traceability of materials and processes is crucial for quality control and future audits.
Structural Integrity
Loading Conditions: Fabrication methods must consider the type of loads (axial, shear, bending, torsional) that the structure will experience.
Fatigue: Repeated loadings can cause micro-fractures that could eventually lead to structural failure.
Residual Stresses: Introduced during the fabrication process, these can affect both the strength and stability of the structure.
Corrosion Resistance: Material choice and coatings are critical to mitigate corrosion, which could severely compromise structural integrity.
Cost
Material Cost: Influenced by the type of steel, market conditions, and bulk ordering.
Labor Cost: Skilled labor is necessary for specialized techniques like welding and machining.
Operating Cost: Includes costs of energy, machinery, and overhead.
Sustainability
Recycling: Steel is 100% recyclable, and new steel often contains recycled steel.
Environmental Impact: Consider the carbon footprint and other environmental impacts of various fabrication methods.

Picture 3: Sustainable Buildings
Codes and Standards
Familiarize yourself with the relevant codes and standards that govern steel design and fabrication, like the AISC (American Institute of Steel Construction) in the United States, or the Eurocode 3 in Europe.
Understanding these elements deeply will empower a structural engineer to make more informed decisions, ensuring the functionality, safety, and durability of the steel structures they oversee.
Eurocode 3 (often denoted as EN 1993) is a European standard for the design of steel structures. It's part of the broader Eurocode system, which covers multiple aspects of civil engineering including design in concrete, timber, and other materials. Eurocode 3 is recognized and implemented across countries in the European Union and has also influenced steel design practices globally.

Key Parts of Eurocode 3
Eurocode 3 is divided into multiple parts, each focusing on different aspects of steel structure design:
EN 1993-1-1: General rules and rules for buildings
Deals with general design rules that are valid for all types of steel structures and specific rules that apply to buildings.
EN 1993-1-2: Structural fire design
Provides principles and requirements for the structural design of steel buildings exposed to fire conditions.
EN 1993-1-3: Cold-formed thin gauge members and sheeting
Specifically geared towards cold-formed steel design.
EN 1993-1-4: Stainless steels
Deals with design rules applicable to stainless steel structural members and sheeting.
EN 1993-1-5: Plated structural elements
Focuses on the design of plated structural components.
EN 1993-1-6: Strength and stability of shell structures
Discusses design aspects related to shell-like structures.
EN 1993-1-7: Plated structures subject to out of plane loading
Focuses on the effects of out-of-plane loading on plated structures.
EN 1993-1-8: Design of joints
Covers the design of fasteners and connections, a critical aspect of structural design.
EN 1993-1-9: Fatigue
Discusses the fatigue design of steel structures exposed to repetitive loading.
EN 1993-1-10: Material toughness and through-thickness properties
Provides rules for materials with constrained conditions, generally related to crack resistance and toughness.
EN 1993-1-11: Design of structures with tension components
Rules for tension members in steel structures.
EN 1993-1-12: Additional rules for the extension of EN 1993 up to steel grades S 700
Rules extended to high-strength steel up to grade S700.
Key Parameters and Variables
Material Factors: Yield strength fy, ultimate strength fu, modulus of elasticity E, and shear modulus G.
Loading: Characteristic and design loads, including combinations.
Limit States: Ultimate Limit State (ULS) and Serviceability Limit State (SLS).
Partial Safety Factors: Applied to both material properties and loads.
Interactions with Other Eurocodes
Given that structural engineering is a multidisciplinary field, Eurocode 3 often interacts with other Eurocodes like Eurocode 0 (Basis of structural design), Eurocode 1 (Actions on structures), and Eurocode 8 (Design of structures for earthquake resistance).
Understanding the complexities of Eurocode 3 is crucial for the design and assessment of steel structures in Europe and serves as a valuable resource for globally recognized best practices.
The importance of a specific part of Eurocode 3 can vary depending on the type of steel structure you are designing, the environmental conditions, and specific design challenges. However, if we were need to pick the most foundational section that serves as a starting point for almost any steel structure design, it would likely be EN 1993-1-1: General rules and rules for buildings.
Why EN 1993-1-1 is Often Considered the Most Important
Broad Applicability: This part lays down the general principles and requirements for the majority of steel structures. Most other parts are specialized extensions or elaborations of the concepts introduced here.
Fundamental Design Principles: It includes key information on material properties, limit states design, and general methodologies that are fundamental to any steel design.
Global Benchmarks: The principles often serve as a reference or baseline for other international design codes.
Design of Elements: The section outlines how to design common structural elements like beams, columns, and slabs using steel, which are fundamental to almost any structure.
Loading Conditions: General load combinations, factoring, and other essential design scenarios are outlined here.
Safety Checks: It provides the guidelines for fundamental safety checks against various limit states, including both the Ultimate Limit State (ULS) and Serviceability Limit State (SLS).
Common Structural Forms: The part is applicable to typical structural forms like building frames, bridges, industrial facilities, and more, making it versatile and commonly referenced.
Compatibility: Concepts and principles laid out in this part are often prerequisites for understanding and implementing the specialized rules given in other parts of Eurocode 3.
That being said, other parts of Eurocode 3 are extremely important for specialized applications. For instance, EN 1993-1-8: Design of joints is crucial for connection design, a critical aspect of structural integrity. EN 1993-1-2: Structural fire design is essential for structures requiring high fire resistance.
So while EN 1993-1-1 serves as a starting point and is perhaps the most universally applicable, the importance of other parts should not be underestimated; they provide vital, specialized information for various aspects of steel design.
About the design of a steel structure step by step
The planning and design of a steel structure is a complex, iterative process that requires a detailed understanding of structural engineering principles, design codes, and real-world constraints. Below is an outline of a typical step-by-step process that a structural engineer might follow for steel structure design:
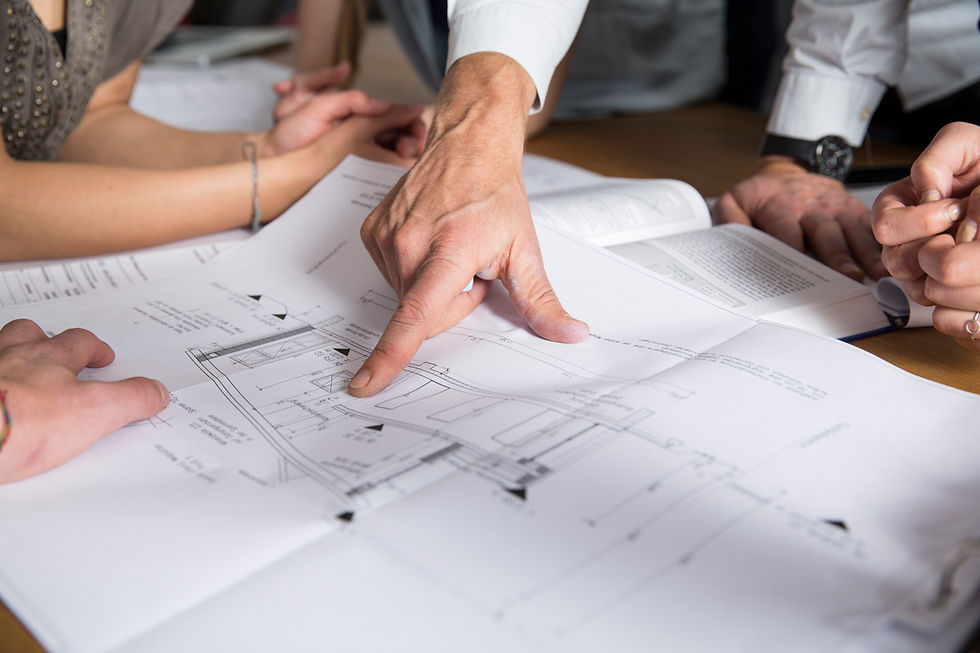
Preliminary Steps
Client Briefing and Scope Definition: Understand the requirements, purpose, and constraints of the project, including budget and timeline.
Site Analysis: Evaluate the site conditions, including soil characteristics, local weather conditions, and possible loadings.
Regulatory Review: Understand and gather all relevant building codes, standards, and regulations applicable to the project, including local amendments to Eurocodes or other international standards.
Conceptual Design Phase
Preliminary Design: Create a conceptual design to identify the type and arrangement of structural elements. This often involves initial sizing and layout drawings.
Load Assessment: Identify all types of loads that the structure will be subjected to, including dead loads, live loads, wind loads, seismic loads, etc., according to relevant codes like Eurocode 0, 1, 3, 8.
Initial Analysis: Perform initial structural analyses to check the feasibility of the conceptual design. This can be done using hand calculations or simplified computational models.
Client and Stakeholder Review: Present the conceptual design to stakeholders for approval and feedback.
Detailed Design Phase
Material Selection: Decide on the types of steel to be used based on design requirements, considering factors like strength, ductility, corrosion resistance, and cost.
Detailed Structural Analysis: Use finite element analysis or other advanced methods to perform a detailed structural analysis. This will involve a more in-depth examination of member sizes, connections, and other elements under different loading conditions.
Design Checks: Conduct design checks for both Ultimate Limit State (ULS) and Serviceability Limit State (SLS) as per relevant parts of Eurocode 3 or other applicable standards.
Connection Design: Design the joints and connections, often referring to Eurocode 3 Part 1-8 or other relevant standards.
Other Details: Design additional details like anchoring, bracing systems, or any specialized structural elements.
Drawings and Specifications: Produce detailed design drawings and specifications, including all dimensions, materials, and construction details.
Peer Review: It's often advisable to have the design reviewed by another experienced structural engineer to identify any possible oversights or improvements.
Client and Stakeholder Approval: Finalize the design after getting the necessary approvals from all relevant parties.
Pre-Construction and Construction Phases
Tendering and Contractor Selection: Prepare tender documents and assist in the selection of a construction contractor.
Fabrication: Oversee or review the steel fabrication process, ensuring all materials and procedures comply with the design specifications and standards.
Construction Oversight: Monitor the construction for adherence to design, including quality of workmanship and materials.
Testing and Commissioning: Conduct or oversee tests on completed structures to ensure they meet all design and safety criteria.
Post-Construction
Handover and Documentation: Once construction is completed and the structure has been tested and commissioned, prepare and handover all relevant documentation to the client.
Post-Occupancy Evaluation: Sometimes performed to assess the behavior of the structure under actual usage conditions, especially for innovative or high-stakes designs.
Maintenance Guidelines: Provide guidelines for regular inspection and maintenance of the steel structure.
Thank you for your time and attention for the topic, see you at the next ones!
Have you checked my blog post called "Deep Talks About Earthquake" ?
Comments